Softwall vs. Hardwall Cleanrooms: Tailoring Environments for Precision Industries
There are two broad categories of cleanrooms. Softwall cleanrooms, often regarded as more temporary solutions, consist of a prefabricated frame and walls made from flexible vinyl sheets. They are known for their adaptability and quick assembly, and are often used in situations where a permanent cleanroom is not necessary or feasible.
Hardwall cleanrooms, on the other hand, are constructed with rigid walls made from materials such as acrylic and offer a stable and controlled environment, making them suitable for applications that require strict adherence to cleanroom standards, such as in medical device manufacturing and biomedical research.
Cleanroom Classifications
Cleanrooms can be certified to various industry standards, including ISO 14644-1. Different industries may have additional specific standards, such as the EU’s GMP (Good Manufacturing Practice) and the USP (United States Pharmacopeia).
ISO cleanroom classifications provide a repeatable methodology for measuring room cleanliness based primarily on the number of particles (of a specific size) present in a cubic meter of air within the cleanroom. The classifications range from the ultraclean ISO Class 1 (a maximum of 10 particles/m³ of size 0.1 µm or larger) to the least strict ISO Class 9 (a maximum of 35.2 million particles/m³ of size 0.5 µm or larger).
Hardwall cleanrooms are capable of achieving the highest classifications (ISO Class 1-4), due to their stable and controlled environment. Softwall cleanrooms, by contrast, are typically only used for lower classifications (ISO Class 5-9) and are more suited for less critical environments. The flexible nature of softwall cleanrooms makes it challenging to maintain the environmental control necessary for the top ISO classifications.
Softwall Cleanrooms
Softwalls are the most convenient option for establishing a clean operating space quickly and are characterized by two primary components:
- Flexible Vinyl Sheet Walls: These sheets are typically transparent or translucent but can be tinted or may come in opaque or UV filtering varieties, including ESD “Static Dissipative” and low outgassing options.
- Prefabricated Frame: The vinyl sheets are hung from a moveable aluminum or steel frame. This modular approach allows for easy assembly and disassembly, catering to the need for temporary cleanroom solutions.
HVAC and Single Pass Airflow
Unlike hardwall cleanrooms that can have recirculating air, softwall cleanrooms typically only employ a single pass system where air is pulled from outside the cleanroom, passed through prefilters and into the HVAC system, and finally expelled through HEPA filters. The air is pushed vertically downward towards the floor and exits underneath the vinyl plastic strip walls, ensuring a continuous flow of filtered air.
Entrances and Contamination Control
Softwall cleanrooms offer a variety of entrance types, including overlapping panels, plastic strip curtains, and hinged doors. The style of entrance significantly impacts the cleanroom’s ability to prevent the ingress of contaminants. For higher classification cleanrooms, additional features like pass-throughs or gowning rooms may be necessary.
Softwall Advantages
- Economical and Quick Installation: The simplicity of their design and the use of lightweight materials like vinyl reduce both the initial investment and the labor costs associated with installation.
- Flexibility and Portability: Softwall cleanrooms can be easily reconfigured, expanded, or relocated to suit changing needs.
- Lower Energy Consumption: Thanks to their lightweight structure and the efficiency of single pass air systems, softwall cleanrooms generally consume less energy compared to hardwall alternatives.
Softwall Disadvantages
- Difficulties in Maintaining Room Pressurization: Due to their flexible vinyl walls, softwall cleanrooms often struggle to sustain a stable, controlled pressure environment compared to hardwall cleanrooms.
- Challenges in Cleaning and Outgassing Issues: The flexible nature of the vinyl walls makes them more difficult to clean thoroughly compared to the rigid surfaces of hardwall cleanrooms. Additionally, new vinyl materials may experience outgassing and release contaminating volatile organic compounds (VOCs) into the cleanroom environment.
- Regulatory Limitations: Softwall cleanrooms are not designed to support positive internal pressure, which is often required for maintaining higher cleanliness standards.
Ideal Softwall Use Cases
Softwall cleanrooms are well-suited for temporary arrangements or situations where flexibility is a priority, including cleanroom applications that require ISO Class 7 or Class 8 environments, such as certain types of laboratory testing, electronics manufacturing, or less critical pharmaceutical processes.
Hardwall Cleanrooms
Unlike with the flexible and removable sheets of a softwall, the walls and ceilings of hardwall cleanrooms are made from rigid panels that are designed for long-term use and finer control of temperature, humidity, and particulates.
Hardwall Advantages
- Permanent and Stable: Their rigid structure is designed to support a long-lasting cleanroom deployment, which is necessary for applications that require a consistently controlled environment over extended periods.
- Enhanced Environmental Control for Strict ISO Classifications: Hardwalls are suitable for the strictest ISO-class cleanroom environments, offering a much higher level of control over particulate and microbial contamination than softwall options.
- Customizability and Adaptability: Despite their permanent nature, hardwall cleanrooms can be tailored to specific spatial and functional requirements, including integration with existing building infrastructure and equipment.
- Convenience of Prefabricated Parts: Hardwall components are typically produced offsite and then assembled at the final location. This approach not only reduces on-site construction time but also minimizes disruption in the existing facility.
- Ease of Cleaning and Strong Durability: The solid construction of hardwall cleanrooms facilitates easier and more effective cleaning, and the durable materials ensure that the cleanroom remains structurally sound and functional over time, resisting wear and tear that could compromise the environment.
Hardwall Disadvantages
- Higher Cost: The cost of a hardwall solution includes not only the materials and construction but also the installation process, which can be more complex and resource-intensive.
- Less Flexibility for Reconfiguration: Modifying or relocating a hardwall cleanroom is more complicated and costly than hanging softwalls or moving a frame on casters, making it less adaptable to changing needs or evolving processes.
- Longer Installation Time: The process often requires specialized labor and coordination with existing facilities, which can lead to longer project timelines.
Ideal Hardwall Use Cases
Hardwall cleanrooms are particularly suited for applications that require a stable environment under extreme conditions or high cleanliness standards. This includes cleanrooms needed in sectors such as medical device manufacturing, life science laboratories, and semiconductor production.
Choosing Between Softwall and Hardwall Cleanrooms
When deciding on a cleanroom, three key factors must be considered:
- Application Requirements: When very strict environmental controls are required, hardwall cleanrooms are the only choice. Softwall cleanrooms can be used for less critical applications, like non-sterile packaging, electronics assembly, or short-term research projects.
- Space and Budget Constraints: Softwall cleanrooms are generally more cost-effective and are adaptable to smaller or irregular spaces. In contrast, hardwall cleanrooms, while requiring a higher initial investment, are more suitable for larger spaces.
- Long-Term vs. Short-Term Needs: Softwall cleanrooms are ideal for temporary or changing needs, whereas hardwall cleanrooms are better suited for permanent installations due to their durability and stability.
CleanSpace helps the world’s most essential companies expand what’s possible for humanity with critical solutions for critical environments. Contact us today to find out what we can do for your organization.
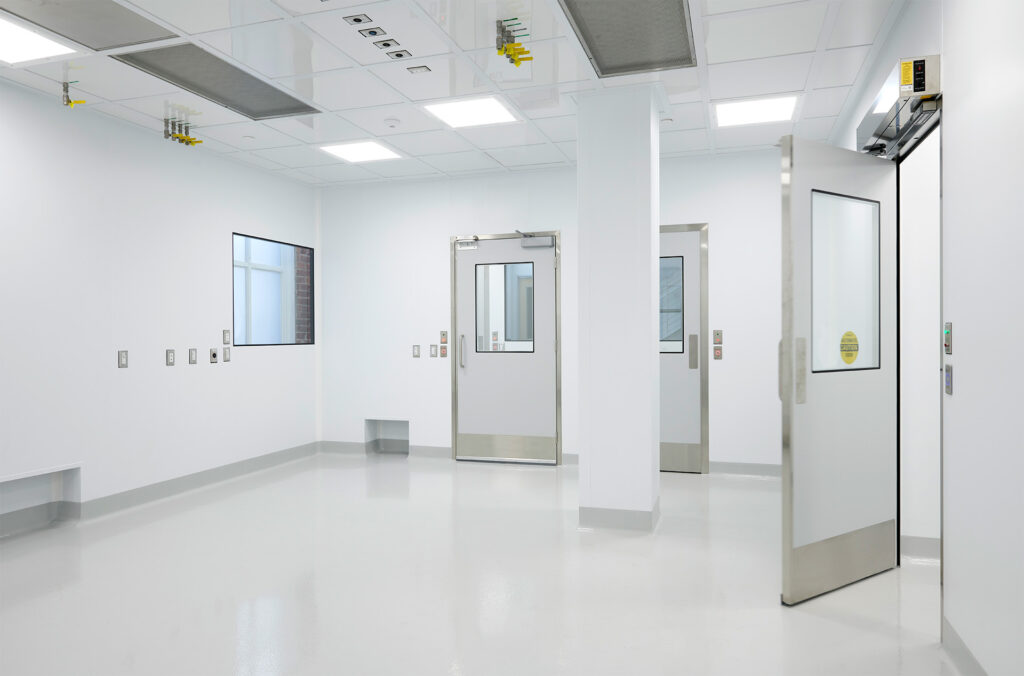