GMP & Modular Cleanrooms
Discover how GMP and modular cleanrooms enhance quality, safety, and efficiency with automation, compliance, and sustainable innovations.
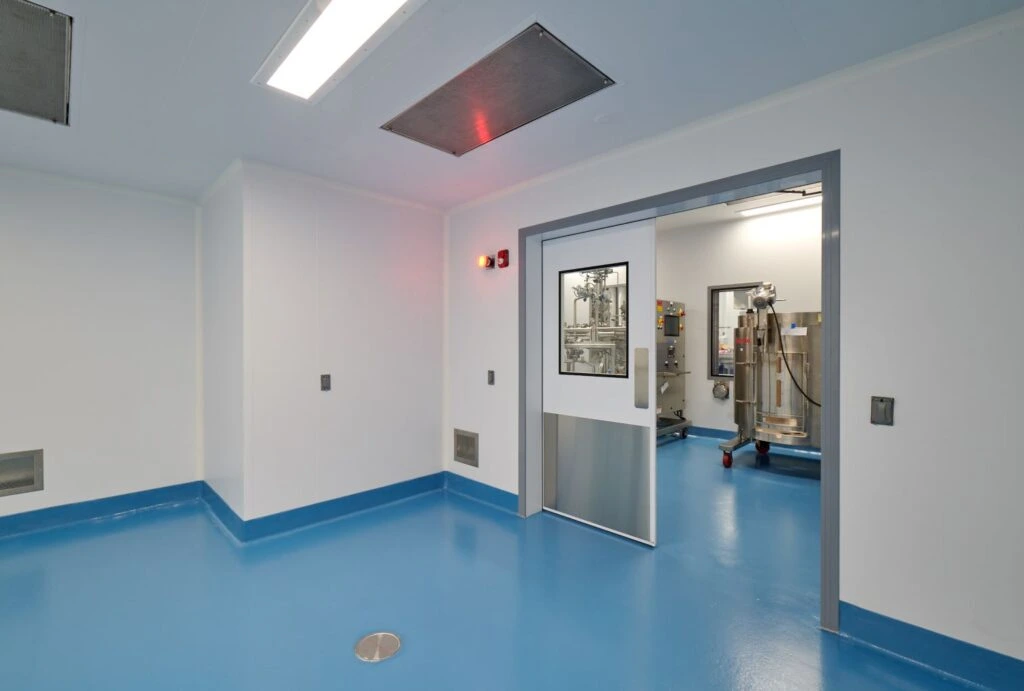
The Rise of GMP: Safeguarding Products, Protecting Consumers
The acronym GMP stands for Good Manufacturing Practice. Its origins lie in the tragedies of the 1950s and 1960s, where poor manufacturing practices led to fatalities and congenital disabilities in pharmaceutical products. The US Food and Drug Administration (FDA) responded by creating regulations outlining good practices for manufacturing, packaging, labeling, and testing drugs and medical devices. These regulations, codified in 21 CFR Part 211, became the foundation of GMP for the pharmaceutical industry.
Over time, GMP expanded to encompass various industries, including biotechnology, food, medical devices, and cosmetics. Each sector developed its specific guidelines, but the core principles remain constant: quality assurance, data integrity, and risk management.
The Evolution of Modular Cleanrooms: Efficiency Meets Control
The development of modular cleanrooms emerged from the aerospace industry in the mid-20th century. The need for controlled environments to build delicate gyroscopes and other sensitive components led to prefabricated cleanroom modules. These modules offered faster construction times, lower costs, and easier expansion than traditional brick-and-mortar cleanrooms.
The technology progressed, and modular cleanrooms gradually found applications in other industries, particularly those requiring stringent contamination control, like pharmaceuticals and microelectronics. Their flexibility and scalability made them attractive for companies seeking to quickly adapt to changing production demands.
Convergence and the Future
Modular cleanrooms and GMP regulations have co-evolved to ensure product safety and integrity. Modern modular cleanrooms are designed to meet stringent GMP requirements, incorporating features like HEPA filtration, controlled air pressure, and specialized flooring.
Where Modular Cleanrooms and GMP Converge:
- Integration of digital tools: Smart modules with sensors and data analytics can optimize cleanroom performance and enhance compliance.
- Advanced automation: Robotics and automated guided vehicles can minimize human intervention and contamination risks.
- Sustainable construction: Eco-friendly materials and energy-efficient designs can reduce the environmental impact of modular cleanrooms.
By leveraging these advancements, the future of modular cleanrooms promises to be even more efficient, sustainable, and compliant with evolving GMP regulations. The collaboration between cleanroom technology and quality assurance practices will continue to safeguard product safety and pave the way for a responsible and innovative future in various industries.
Building Beyond Cleanliness: Safeguarding Process and Product Integrity in Modular Cleanrooms
Modular cleanrooms offer a faster, more efficient alternative to traditional cleanroom construction, particularly in industries like pharmaceuticals, biotechnology, and microelectronics, where stringent contamination control is paramount. However, simply achieving a pristine environment isn’t enough. Ensuring product and process integrity requires meticulous planning and adherence to Current Good Manufacturing Practices (GMP) across all aspects of your modular cleanroom operation. Oversight requires attention to personnel, process, and material flows, each holding unique challenges and opportunities.
Personnel Flow: Choreographed Movement for Contamination Control
Personnel movement is a significant source of contamination risk in cleanrooms. Optimizing personnel flow requires a thorough understanding of GMP protocols and risk-based zoning. Carefully designed entry and exit procedures are crucial, including gowning protocols and air showers. Implementing unidirectional flow paths can further minimize cross-contamination, especially in critical areas. Advanced access control systems and training programs focused on aseptic technique play a vital role.
Process Flow: Streamlining Efficiency without Compromising Integrity
The efficiency and safety of your cleanroom operation hinges on well-defined process flows, and by applying lean manufacturing principles, you can minimize unnecessary movement and optimize equipment placement. Integrating advanced process automation wherever feasible can further reduce contamination risks associated with human interventions. However, it’s crucial to consider potential automation failures and ensure seamless manual interventions when necessary. Validation of both manual and automated processes underpins the integrity of your operations.
Material Flow: Minimizing Contamination Pathways
Material flow within the cleanroom must be carefully managed to prevent contamination and ensure product quality. Establishing designated pathways for different material types, implementing a double-door airlock system for material entry and exit, and utilizing closed-loop transfer systems whenever possible are essential practices. Traceability is also important, with robust material handling procedures and tracking systems ensuring complete control.
The Impact of Automation and Digitization
Automation and digitization can significantly impact personnel and material flow within modular cleanrooms. Automated guided vehicles (AGVs) and robotic arms can minimize human contact with critical materials and equipment, reducing contamination risks. Digital twins can facilitate process optimization and real-time monitoring, enhancing control and efficiency. However, it’s essential to consider the potential drawbacks, such as cybersecurity threats and the need for robust validation of automated systems. Research in this area is particularly pertinent to exploring the optimal balance between automation and human oversight in ensuring cleanroom integrity.
Environmental Sustainability: Building Clean, Thinking Green
While ensuring product and process integrity is paramount, environmental sustainability should be considered. Modular cleanroom construction offers inherent advantages. Prefabrication in controlled environments minimizes on-site waste and dust generation. Additionally, modular panels typically employ recyclable materials and require less energy and resources for construction than traditional methods. Moreover, energy-efficient cleanroom design, including optimizing air filtration and HVAC systems, can significantly reduce operational energy consumption.
Conclusion: A Holistic Approach to Modular Cleanroom Excellence
Building and operating modular cleanrooms goes beyond achieving a clean environment. Safeguarding product and process integrity requires a holistic approach that integrates GMP compliance, optimized flow management, and a thoughtful consideration of emerging technologies like automation and digitization. By prioritizing quality and sustainability, you can ensure your modular cleanroom delivers immaculate products and a responsible and ethical operational footprint.
The future of modular cleanrooms is bright, and CleanSpace US is at the forefront, pushing the boundaries of innovation and sustainability. We’d love for you to join us on this journey – explore our website to dive deeper into the latest trends and insights, and connect with us on LinkedIn for industry discussions and exciting updates. Together, let’s build a future where immaculate products and sustainable practices go hand-in-hand!
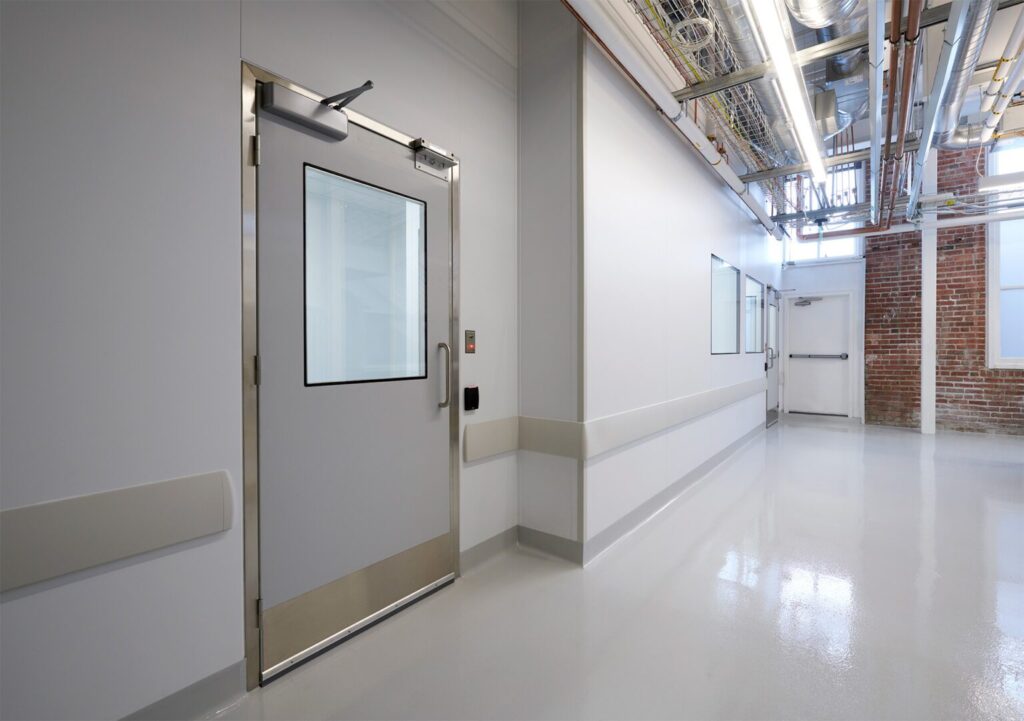