Cleanrooms, Cold Rooms, & Dry Rooms
Learn the differences between dry and cold rooms, their roles in research, pharma, and manufacturing, and how modular cleanrooms adapt to industry demands.
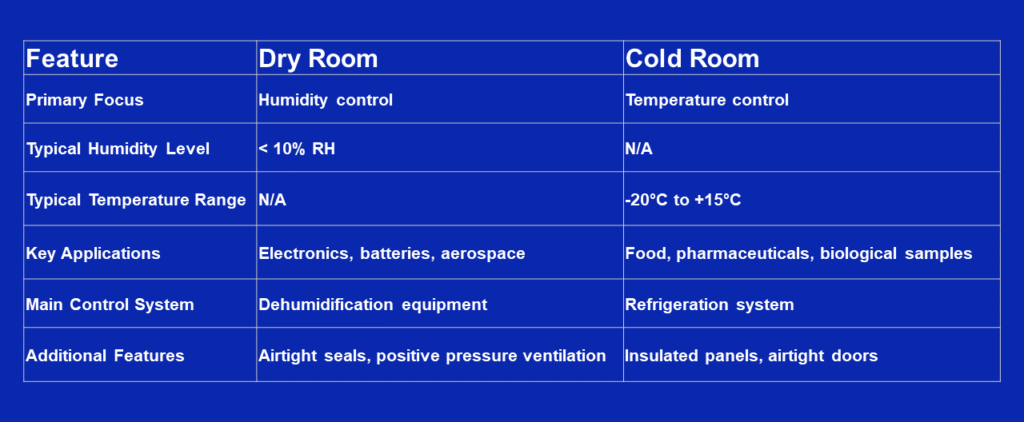
In this post, we are looking into the world of controlled environments to discover the intricacies of two distinct yet vital spaces – dry and cold rooms. These controlled environments play crucial roles in various industries, from scientific research to manufacturing and pharmaceuticals. So, if you’ve ever wondered about the differences, applications, and principles governing their operations, you’re in the right place.
A dry room and a cold room are two distinct controlled environments used for specific purposes in various industries, particularly in scientific research, manufacturing, and pharmaceuticals. Understanding these environments requires knowledge of their respective characteristics, applications, and the principles that govern their operations.
Dry Room
A dry room, also known as a cleanroom or controlled environment, is a specialized facility designed to maintain extremely low levels of airborne particulate contamination and precise control over temperature, humidity, and other environmental factors. These environments are essential in industries where even minor contamination can harm product quality, research results, or manufacturing processes. Here are key aspects to understand about dry rooms:
Cleanliness Levels: Cleanrooms are classified into different cleanliness levels based on the number of airborne particles per cubic meter. ISO standards typically determine the classification, with ISO 14644-1 being a widely accepted reference. Class 1 represents the cleanest environment with the fewest particles, while Class 9 has the highest allowable particle
count.
Environmental Control: Dry rooms require strict control over environmental factors, which includes maintaining stable temperature and humidity levels, controlling air pressure differentials, and often using high-efficiency particulate air (HEPA) or ultra-low penetration air (ULPA) filters to remove contaminants from the air.
Applications: Dry rooms are used in various industries, including semiconductor manufacturing, pharmaceutical production, aerospace, electronics, and biotechnology. They ensure product quality and reliability by preventing contamination during manufacturing or research processes.
Personnel and Equipment: Operators in dry rooms typically wear specialized cleanroom garments, including coveralls, gloves, and masks, to minimize human contamination. Equipment used in these environments is carefully selected and designed to reduce particle generation.
Entry and Exit Protocols: Strict protocols are in place for entering and exiting dry rooms to prevent contamination. These often include air showers, gowning rooms, and adhesive mats to remove particles from footwear.
Cold Room
A cold room also called a temperature-controlled room or cold storage facility, is designed to maintain specific low temperatures for storing perishable items, such as food, pharmaceuticals, biological samples, and certain chemicals. Unlike dry rooms, cold rooms primarily focus on temperature control and are less concerned with particulate contamination. Here are key aspects to understand about cold rooms:
Temperature Control: Cold rooms maintain temperatures lower than the surrounding environment. Standard temperature ranges for cold rooms vary from -20 °C to 4°C, depending on the specific storage requirements.
Humidity Control: Humidity levels in cold rooms are typically higher than those in dry rooms to prevent the dehydration of stored products. Maintaining humidity prevents the formation of ice crystals on sensitive items.
Applications: Cold rooms are used extensively in the food industry for storing perishable goods, in pharmaceuticals for storing temperature-sensitive medications, and in research for preserving biological samples, chemicals, and reagents.
Insulation and Refrigeration Systems: Cold rooms are well-insulated to prevent temperature fluctuations. They are equipped with refrigeration systems that maintain the desired temperature range consistently.
Shelving and Racking: Cold rooms use shelving and racking systems optimized for storing different products. These systems maximize storage capacity and allow for efficient organization.
A dry room is a controlled environment that maintains low particulate contamination levels and precise control over environmental conditions. Their primary use is in industries where contamination can be detrimental. In contrast, a cold room is a temperature-controlled storage facility used for preserving perishable items, mainly focusing on temperature and humidity control. Understanding the distinctions between these environments is essential for those involved in industries where their applications are critical.
Can modular cleanrooms be only cold or dry?
Modular cleanrooms are versatile, prefabricated structures that offer the advantage of adaptability to different environmental conditions.
Modular Cleanrooms for Cold Applications:
Modular cleanrooms can be designed and equipped as cold rooms for storing temperature-sensitive materials or products. This configuration entails specific considerations:
Temperature Control
Modular cleanrooms have refrigeration systems capable of maintaining the desired low temperatures within the prescribed range to serve as a cold room. These systems are integrated into the cleanroom’s structure to ensure precise temperature control.
Insulation
Adequate insulation is crucial to configuring a modular cleanroom as a cold room. Insulation materials with high thermal resistance prevent heat exchange with the external environment, thus maintaining cold storage conditions.
Humidity Management
Cold rooms require careful humidity control to prevent the formation of ice crystals on stored items. Cleanroom design may incorporate humidity control systems, such as humidifiers, to maintain suitable humidity levels.
Sealing and Airflow
The cleanroom’s design ensures airtight sealing to minimize temperature fluctuations and prevent the ingress of warm air. Proper airflow management maintains temperature uniformity throughout the cold room.
Shelving and Racking
Interior configurations include shelving and racking systems optimized for storing products at low temperatures. These systems are designed to accommodate various items while maximizing storage capacity.
Modular Cleanrooms for Dry Applications:
Conversely, modular cleanrooms can be configured as dry rooms, also known as cleanrooms or controlled environments, to maintain low levels of particulate contamination and precise control over environmental factors. Critical considerations for configuring modular cleanrooms for dry applications include:
Cleanliness Levels
The cleanroom must adhere to specific cleanliness classifications defined by industry standards (e.g., ISO 14644-1). Airborne particle counts must be rigorously controlled and monitored.
Environmental Control
The cleanroom design includes temperature and humidity control systems and air filtration using HEPA or ULPA filters. The maintenance of stable environmental conditions is paramount.
Personnel and Equipment
Operators within the cleanroom wear specialized cleanroom attire to minimize human contamination. Equipment and furnishings are selected and designed to reduce particle generation.
Entry and Exit Protocols
Strict personnel entry and exit protocols, such as air showers and gowning rooms, are implemented to prevent contamination.
Modular cleanrooms can indeed be configured to function as either cold rooms or dry rooms, depending on the industry’s specific requirements or application. These configurations involve integrating different systems and considerations to achieve the desired environmental conditions, be it precise temperature control for cold storage or stringent particulate contamination control for cleanroom applications. The adaptability of modular cleanrooms makes them a versatile solution for various industries where controlled environments are essential.
How else can modular cleanrooms be configured?
Modular cleanrooms, while often associated with dry or cold environments, can be configured to serve purposes other than dry or cold applications. The versatility of modular cleanroom design allows for customization to suit a wide range of specific industry needs and environmental requirements. In this academic-style explanation, we will explore the concept of modular cleanrooms beyond dry and cold applications.
Modular Cleanrooms for Non-Dry and Non-Cold Applications
Pharmaceutical Manufacturing
Modular cleanrooms are frequently employed in pharmaceutical manufacturing processes that require a controlled environment to ensure product quality and compliance with regulatory standards. These cleanrooms may not necessarily be cold or dry but are designed to maintain stringent cleanliness levels, control airborne particulate contamination, and provide environmental conditions suitable for pharmaceutical production.
Biotechnology and Research
Research laboratories, particularly those involved in biotechnology and life sciences, utilize modular cleanrooms to create controlled experiments, testing, and research environments. These cleanrooms are tailored to maintain cleanliness and control temperature, humidity, and other relevant environmental factors as required by the specific experiments or procedures.
Electronics Manufacturing
In electronics manufacturing, cleanrooms prevent contamination of sensitive electronic components during assembly. These cleanrooms may not always be cold or dry, but they prioritize particle control and electrostatic discharge (ESD) prevention to ensure the quality and reliability of electronic products.
Aerospace and Precision Engineering
Industries like aerospace and precision engineering rely on modular cleanrooms to safeguard the manufacturing and assembly of critical components. These cleanrooms are designed to minimize particulate contamination and maintain controlled environmental conditions, which may not necessarily involve extreme cold or dryness.
Food Processing
While not typically associated with cold storage, modular cleanrooms can be adapted for specific food processing applications that require a controlled environment to meet food safety standards. These cleanrooms focus on cleanliness and hygiene rather than temperature control.
Medical Device Manufacturing
Cleanrooms used in medical device manufacturing prioritize contamination control and adherence to regulatory standards. They are tailored to the specific requirements of medical device production and may sometimes be cold or dry.
Semiconductor Fabrication
Although semiconductor manufacturing cleanrooms often require precise temperature control, they can also be configured for other semiconductor-related processes that prioritize particle control and cleanliness but do not necessitate cold or dry conditions.
Wrapping Up
Modular cleanrooms can be designed and customized for various applications beyond dry or cold environments. The adaptability of modular cleanroom technology allows industries to create controlled environments that address their specific needs, whether it pertains to cleanliness, temperature, humidity, or other critical factors essential for their operations. As such, modular cleanrooms represent a versatile solution for industries with diverse requirements for controlled environments.
The adaptability of modular cleanrooms makes them an invaluable solution for creating controlled environments that ensure product quality, safety, and compliance with industry standards. So, as industries evolve and new challenges arise, remember that modular cleanrooms stand ready to meet the ever-changing demands of controlled environments, providing adaptable solutions for a cleaner, safer, and more precise future.