5 Innovative Applications of Modular Cleanrooms in the Cell & Gene Industry
Learn how modular cleanrooms revolutionize ATMP manufacturing by reducing costs, accelerating production, and ensuring compliance for life-saving therapies.
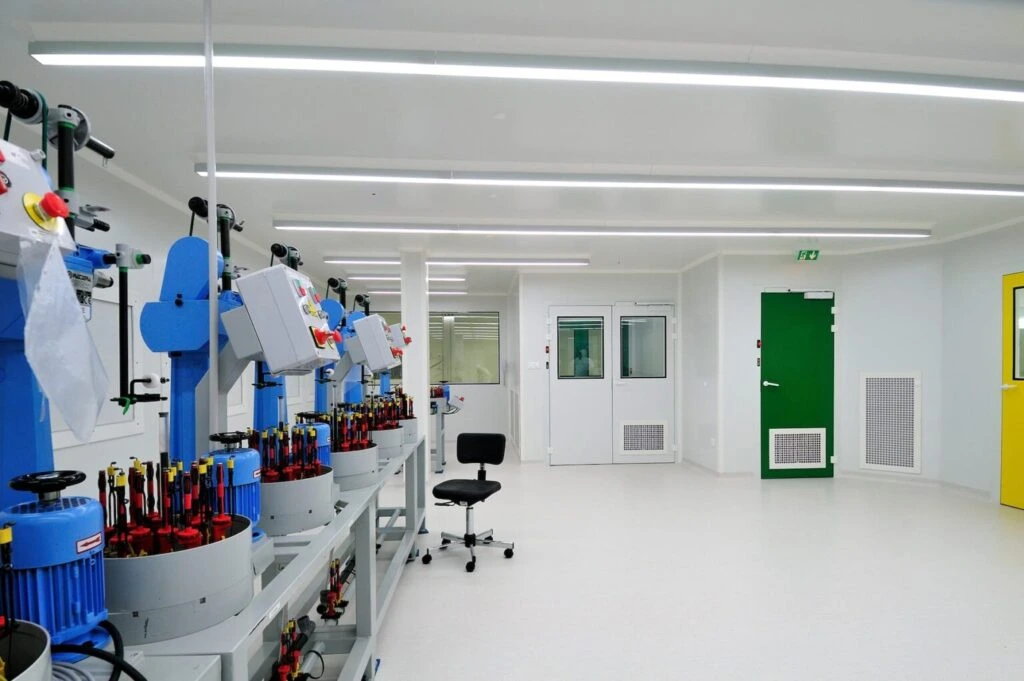
The term Advanced Therapy Medicinal Products (ATMPs) officially emerged in 2007, with the adoption of Regulation (EC) No 1394/2007 by the European Commission. This regulation established a legal framework for these innovative therapies in the European Union.
However, the concept and development of ATMPs have a more extended history, tracing back to earlier forms of cell and gene therapies that emerged in the 1980s and 1990s. These earlier therapies, often called gene therapy, somatic cell therapy, or tissue-engineered therapies, faced regulatory challenges due to their novelty and complexity.
The introduction of the ATMP terminology in 2007 represented a significant step forward by recognizing these therapies as a distinct category with specific regulatory requirements. This categorization facilitated their development and approval by providing a clear framework for manufacturers and regulators.
Here’s a brief timeline of the evolution of ATMPs:
- 1980s-1990s: Early development of cell and gene therapies.
- 1990s-2000s: Regulatory challenges and growing interest in these therapies.
- 2007: Adoption of Regulation (EC) No 1394/2007, introducing the term “ATMPs” and a dedicated regulatory framework in the EU.
- 2012: The Food and Drug Administration (FDA) adopted a similar regulation in the US under the 21st Century Cures Act.
- Present: Continued development and an increasing number of approved ATMPs for various diseases.
As research progresses and regulatory processes become more streamlined, ATMPs are expected to grow significantly in the coming years, offering new hope for treating various diseases.
ATMPs & Modular Cleanrooms
Advanced Therapy Medicinal Products (ATMPs) hold immense promise for treating a wide range of diseases, offering personalized solutions with the potential to cure once-untreatable conditions. However, the complex manufacturing process for these therapies often needs to be improved due to stringent regulations and lengthy construction times for traditional cleanroom facilities. This convergence is where modular cleanroom solutions emerge as game-changers, poised to expedite production and deliver life-saving treatments to patients faster.
The Challenges of Traditional Cleanrooms:
Building a cleanroom from scratch, often called “stick-built,” is time-consuming and expensive. It can take 12-18 months or more to complete, involving multiple contractors and complex construction workflows. This delay translates to wait times longer for patients desperately needing these therapies.
The Advantages of Modular Cleanrooms:
Modular cleanrooms offer a prefabricated, pre-engineered alternative. These cleanrooms are built off-site in standardized sections, allowing for faster assembly and installation, typically within 3-6 months. The preparation and speed translate to significant time and cost savings, along with:
- Enhanced flexibility: Modular components can be easily reconfigured or expanded to adapt to changing needs.
- Superior quality control: Manufactured in controlled environments, modular cleanrooms offer consistent quality and reduced risk of contamination.
- Simplified validation: Standardized designs expedite the validation process required for regulatory compliance.
Impact on ATMP Production:
Reduced Time to Market:
- Traditional cleanrooms: 12-18 months of construction time means delayed availability of life-saving treatments.
- Modular cleanrooms: 3-6 months of construction time enables faster deployment of production facilities, potentially saving lives through earlier access to therapies.
- Example: Penn Medicine established its cell and gene therapy program significantly faster using a modular cleanroom solution.
Increased Production Capacity:
- Traditional cleanrooms: Expanding production requires constructing new facilities, a lengthy and expensive process.
- Modular cleanrooms: Standardized modules allow for easy expansion or reconfiguration, adapting to growing production demands without significant delays.
- Impact: Modular cleanrooms help manufacturers meet the increasing demand for ATMPs, making these therapies more accessible to patients.
Minimized Operational Costs:
- Traditional cleanrooms: High construction and maintenance costs burden manufacturers.
- Modular cleanrooms: Lower initial cost due to prefabrication and reduced on-site labor. Additionally, their standardized design facilitates efficient cleaning and maintenance, minimizing long-term costs.
- Benefit: Cost savings enable manufacturers to invest more in research and development, accelerating advancements in the field.
Beyond these core benefits, modular cleanrooms offer several additional advantages for ATMP production:
- Enhanced Quality Control: Manufactured in controlled environments, modular units minimize contamination risks compared to traditional construction.
- Improved Regulatory Compliance: Standardized designs ease validation processes required for regulatory approval.
- Flexibility and Scalability: Modular components can be adapted to specific workflows and future needs, offering long-term value for manufacturers.
- Sustainability: Prefabrication often uses recycled materials and reduces construction waste, promoting environmentally friendly practices.
The Future of ATMP Manufacturing:
The future of ATMP manufacturing gleams with immense potential, promising personalized treatments for an array of previously untreatable conditions. And at the forefront of this revolution stand modular cleanrooms, poised to accelerate progress and deliver hope to countless patients.
As researchers delve deeper into gene editing, chimeric antigen receptor (CAR) T-cell
therapies, and other innovative approaches, the demand for ATMPs will undoubtedly surge. With their agility and scalability, modular cleanrooms will be instrumental in meeting this demand rapidly and cost-effectively.
Beyond speed, the future of ATMP manufacturing emphasizes decentralization, bringing production closer to patient populations. Modular cleanrooms will be well-suited for establishing smaller, geographically dispersed facilities thanks to their transportability and adaptability. This distribution can further expedite treatment access and optimize logistics.
Furthermore, integrating automation and intelligent technologies into modular cleanrooms holds immense promise. Automated processes can ensure consistency, minimize human error, and improve data collection, while intelligent monitoring systems can optimize production efficiency and resource utilization.
Overall, the future of ATMP manufacturing paints a picture of personalized, accessible, and efficient therapies. Modular cleanrooms, seamlessly blending with advancements in automation and data science, will be the cornerstone of this transformation, paving the way for a brighter future for patients and the healthcare industry.
Conclusion
The promise of modular cleanrooms stretches far into the future, and CleanSpace US is actively shaping that horizon. We’re not just innovating – we’re pushing the boundaries to ensure a sustainable future for this transformative technology.
This journey isn’t meant to be walked alone. Please explore our website to stay ahead with the latest trends and insights. Join the conversation on LinkedIn, where we share industry discussions and exciting updates. Let’s build a future where cutting-edge products and responsible practices are inseparable.